The last thing you want is your paving order to arrive damaged. This is what we do to ensure it arrives in perfect condition.
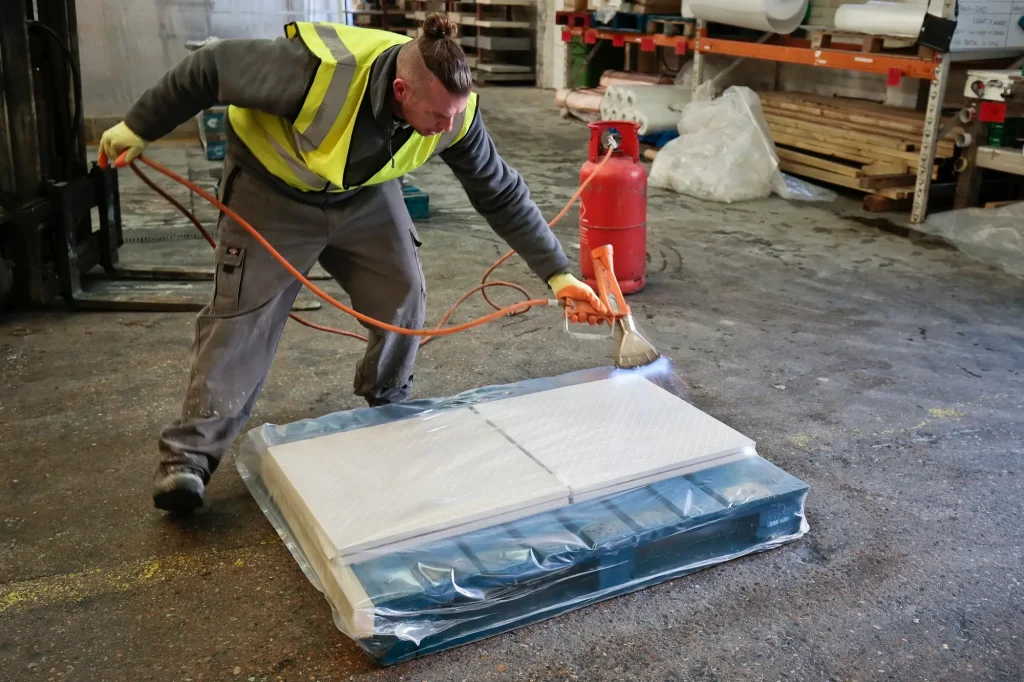
Why we need to protect paving
For something so heavy and solid, it seems strange that stone can be so fragile. But there it is. Sawn stone, like sandstone and limestone, is susceptible to chips because of the way it’s cut. When stone is sawn, the edges are very sharp, which means they can be easily damaged. This is one reason why step treads, coping and pier caps are given an edge profile.
Our challenge is therefore to reduce the chances of stone becoming chipped as much as possible and, like any other challenge, it’s a great opportunity for some innovation and creative problem solving.
In our Bespoke Stone Centre, we've evolved our packing methods considerably since we began. It seems a lifetime ago that we used to stack slabs or step treads directly on top of each other and protect with a swathe of cling wrap.
Special supports
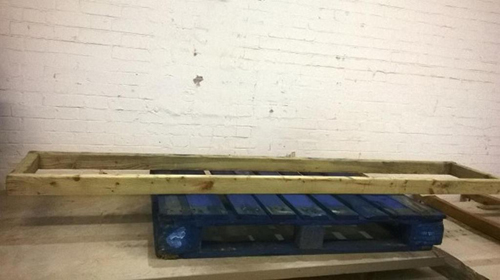
Now, there are several methods that we use to protect the stone. For example, the ends of long step treads are particularly vulnerable to damage when they are overhanging the edges of a pallet, so now we use timber frames to support the full length of the stone. Simple but very effective!
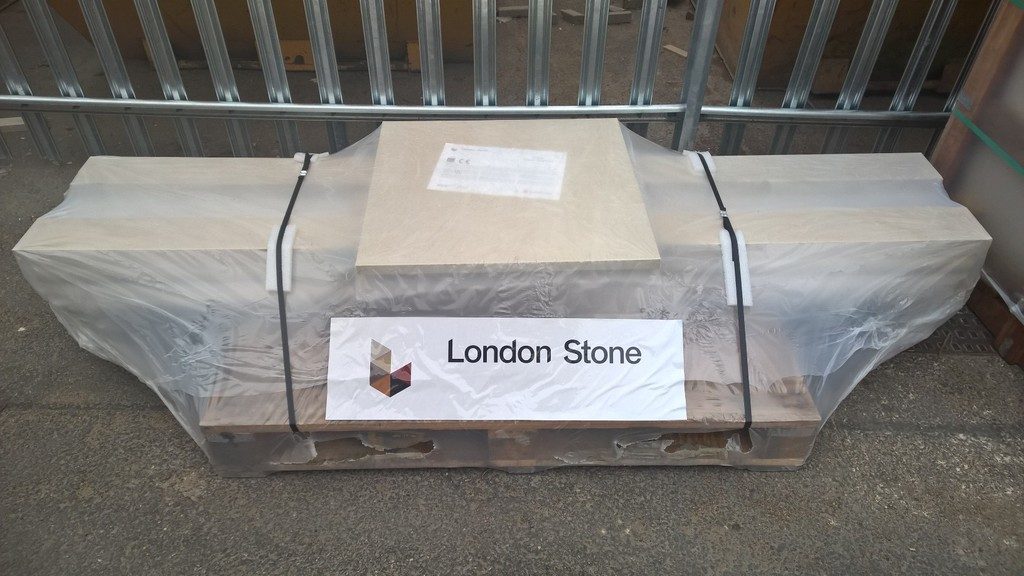
Foam padding
Some time ago we learned the best approach to keeping paving slabs and bespoke items in excellent condition is to use foam, and not just any old foam; use the wrong product and it stains the paving. Depending on the size of the items, we use either small spacers or whole sheets laid between the slabs. This keeps the slabs apart and makes them easier to separate and lift at the other end. The only exception to this is when we pack fixed-width, random-length paving, which we find remains more stable if packed without spacers.
Strapped into place
Once the stone is stacked, we stabilise it. You can see in our video how we use tension banding straps and wrap the whole in heat wrap.
Some might accuse us taking too much of a belt-and-braces approach, but over the years we've substantially reduced the number of jobs where damage is sustained en route to the site. This means that customers are happy and we're happy.
Taking pains like these result in no small outlay. Heat-shrink equipment is surprisingly expensive, and the number of spacers we get through has to be seen to to be believed, but we've reached the stage where we've got packing down to as fine an art as possible.
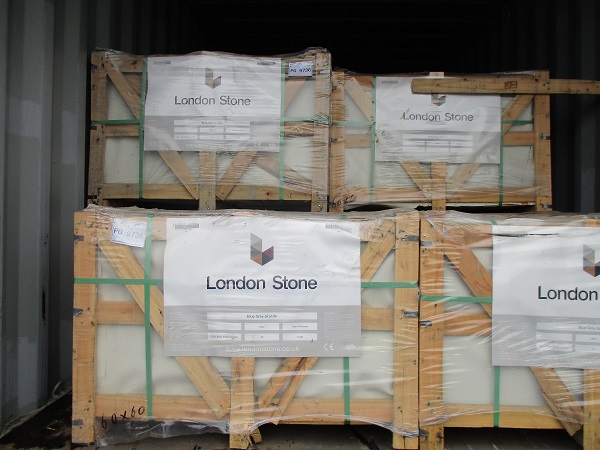
And heat shrink has another advantage: a nice smooth surface on which to stick labels securely. All our paving comes with a sticker on the front, so you can immediately see which stone is ours after you've unloaded. It looks good, too.
Improving packaging from suppliers
When we first started importing stone, we realised the importance of packing throughout the supply chain.
Take Indian sandstone paving, for example. Crates of stone packaged in the stone regions of Kota and Gwalior need to be transported to Mundra Port, a journey which can take three days on roads that are unfit for purpose.
Stone crates weigh on average a ton each, which places a tremendous burden on the wooden crates. Any weak spots in the crate material or crate construction are quickly exposed. Crates start to lean to one side and the resulting movement in their load of stone slabs leads to damage. Nails are also a problem, when stone rubs against nails during transit it can quickly become damaged.
Sawn paving presented huge problems when we first started. We had particular problems with our Beige Sawn Sandstone Paving. Nails in the crates would rust and this rust would then slowly dribble down onto the stone. Such was the extent of this problem that we began to store our sawn paving indoors.
Reducing environmental impact
We’ve spent countless hours with our staff and suppliers, discussing ideas of how we can improve packaging. And we welcome feedback from our clients.
Our drive to reduce carbon emissions makes us assess every part of our production line at regular intervals. Our emphasis on the importance of our business on the environment is something that has been enthusiastically received at our An Evening with London Stone events. Clients have been nothing but encouraging and are now telling us they are looking into how to reduce their own environmental impact.
Reducing packaging is an ongoing goal. This not only reduces our impact on the environment, but also means less for our customers to dispose of on site and reduces costs. Some, like heat wrap, is extremely difficult to find an effective replacement for, but overall we have begun reducing the amount of packaging we use already.
Poor packaging will soon be found out during transportation. So, when you next see a crate of stone, take a look. If the crate is tilting or leaning to one side, then there is a high chance that some of the paving inside will be damaged. If the crate looks in good condition, there is every chance that the stone inside will be in equally good condition – proof that it’s been packaged by someone who genuinely cares about the stone they’re packing.
Post updated: August 2023